Butterfly valve seal material PTFE and EPDM difference
Date: 2025-07-12 Categories: Valve knowledge Views: 1589
Excerpt:
This article compares the performance differences and application scenarios of two key sealing materials for butterfly valves, PTFE (polytetrafluoroethylene) and EPDM (ethylene propylene diene rubber). PTFE is known for its excellent chemical stability, corrosion resistance (acid and alkali/solvent resistance) and low coefficient of friction, and is widely used in the chemical, petroleum, pharmaceutical and other industries, but its mechanical strength is weak and caution is required at high temperatures. epdm, on the other hand, possesses excellent weatherability ( Aging, ozone, high temperature, water vapor) and insulation, especially suitable for outdoor piping, waterproofing and electrical applications, but its chemical stability is relatively weak compared to PTFE. When choosing, it is necessary to weigh the characteristics of the two according to the specific working conditions (fluid characteristics, environmental conditions) to optimize the performance and life of the butterfly valve.
butterfly valveAs a key component of fluid control, the choice of sealing material is directly related to the performance and service life of butterfly valves. In the butterfly valve sealing material, polytetrafluoroethylene (PTFE) and EPDM rubber (EPDM) are two common and excellent performance of the material, but they each have unique characteristics and applicable scenes. The difference between PTFE and EPDM in butterfly valve sealing material is as follows:
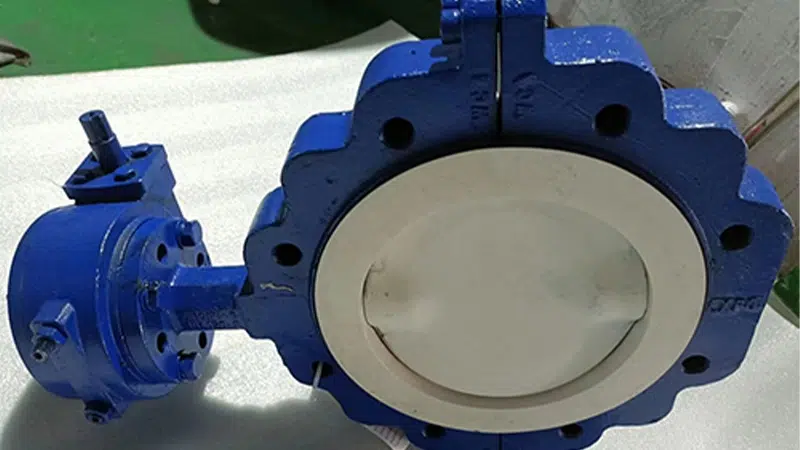
Polytetrafluoroethylene, or PTFE for short, is highly regarded for its excellent chemical stability, high and low temperature resistance. Its extremely low coefficient of friction, excellent self-lubricating ability and non-stick characteristics ensure that PTFE-sealed butterfly valves can maintain a smooth flow in the process of fluid transportation, greatly reducing friction loss. Moreover, PTFE sealed butterfly valves have excellent corrosion resistance and can resist the erosion of many acids, alkalis and organic solvents, which is why they are widely used in chemical, petroleum, pharmaceutical and other industries.
Despite its many advantages, PTFE has some limitations. For example, it has relatively weak mechanical strength and is susceptible to damage from external forces. In addition, PTFE can release harmful gases at high temperatures, so care must be taken when using it in certain environments.
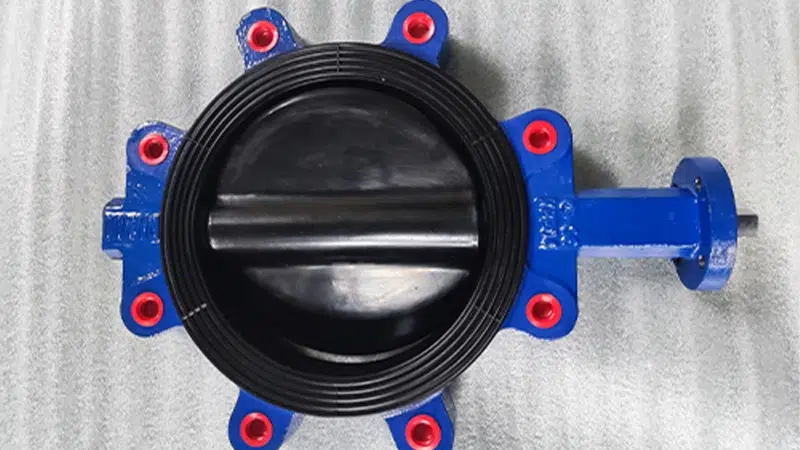
In contrast, EPDM rubber is very popular in the market due to its excellent resistance to aging, ozone, high temperature and water vapor. Even in harsh environments such as high temperatures, high humidity, and strong ultraviolet rays, EPDM-sealed butterfly valves can maintain the stability of their performance, thus demonstrating their extensive use in outdoor applications such as pipelines and waterproof layers. In addition, EPDM-sealed butterfly valves have excellent insulation properties, making them ideal for applications requiring high electrical performance.
However, compared with PTFE sealed butterfly valves, EPDM sealed butterfly valves are slightly insufficient in chemical stability, and their resistance to certain strong acids, alkalis and other chemicals is relatively weak. Therefore, when selecting the sealing material for butterfly valves, the specific use environment and fluid characteristics must be considered comprehensively.
On the whole, PTFE and EPDM butterfly valves have different performance characteristics and scope of application. In actual operation, we must make a choice based on specific needs and the actual situation, so as to maximize the advantages of different sealing materials butterfly valves, to ensure efficient and reliable fluid control.